
NDT & NDT Inspection
Non-Destructive Testing (NDT) is a broad set of analysis techniques used in the science and technology industry to evaluate the properties of a material, component, or system without damaging it. The terms "non-destructive testing" (NDT), "non-destructive testing inspection" (NDI), and "non-destructive testing evaluation" (NDE) are also commonly used to describe this technology.

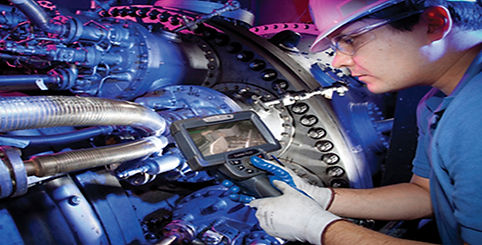
Because NDT does not permanently change the article under review, it is an invaluable technique that can save both money and time in product evaluation, troubleshooting, and research. Common NDT methods include ultrasonic, magnetic particles, liquid penetrating, radiographic, and remote visual inspection (RVI).
It is widely used in the fields of machinery, petroleum, electricity, construction, systems, aviation, medicine, and art.
NDT is used in a variety of environments spanning a wide range of industrial activities, with new NDT methods and applications continually being developed. Non-destructive testing methods are routinely applied in industries where the failure of a component would cause significant hazards or economic losses, such as transport, pressure vessels, construction structures, piping, and lifting equipment.
RT (radioactive test):
Radioactive radiation with some properties emanating from a controllable radiation source is emitted as it passes through the test piece. If there are discontinuities in the areas where it passes, the discontinuities are shown on the photographic film in a different color.

Ultrasonic Examination (UT):
Ultrasonic testing is used to identify defects in metal workpieces (even if they are deep), especially when RT is not possible or accurate, as with thick parts (> 8 mm) and some joints. forms (HV/DHV-sewn T joint). It can also be used for lamination control of metal sheets.

Liquid Penetrant Test (PT):
It is a frequently used method for the determination of discontinuities on the workpiece surface. The main principle of PT is that the penetrating liquid has a strong contrasting effect that makes discontinuities in a workpiece more pronounced.

A Magnetic Particle Test (MT):
It is used to detect surface and near-surface discontinuities in ferromagnetic materials. The basic principle is to magnetize test equipment by directly transmitting alternating and direct current or magnetic field lines. If there is any discontinuity in any part of the part under test, the magnetic field lines deviate from the discontinuity due to the permeability differences, and a very dense leakage field is formed on the discontinuity.
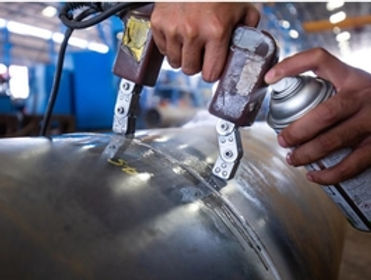